
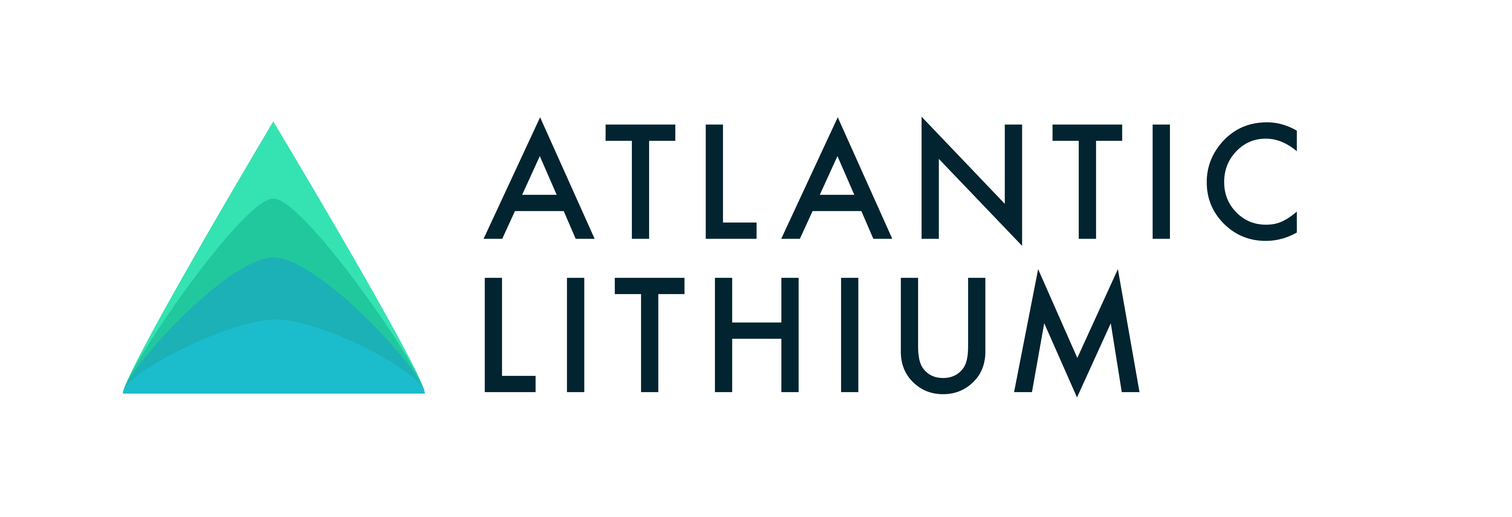
30 July 2024
New Dog-Leg Target Delivers Increase to Ewoyaa MRE
Drilling at the new Dog-Leg target increases the Mineral Resource Estimate
for the Ewoyaa Lithium Project to 36.8Mt at 1.24% Li2O
Atlantic Lithium Limited (AIM: ALL, ASX: A11, GSE: ALLGH, OTCQX: ALLIF, "Atlantic Lithium" or the "Company"), the African-focused lithium exploration and development company targeting to deliver
Highlights:
- Total Mineral Resource Estimate for the Company's flagship Ewoyaa Lithium Project increased to 36.8Mt at 1.24% Li2O, reported in accordance with the JORC Code (2012).
- 81% of the Total Resource now in the higher confidence Measured and Indicated categories (3.7Mt at 1.37% in the Measured category, 26.1Mt at 1.24% in the Indicated category and 7.0Mt @ 1.15% Li₂O in the Inferred category).
- MRE increase follows targeted drilling programme, undertaken in 2023 and H1 2024, comprising sterilisation drilling to support the plant and haul road design and resource conversion drilling, converting Inferred resources to Indicated and Measured resources, to provide mine plan optionality; new Dog-Leg target identified through this process.
- Drilling subsequently undertaken on the Dog-Leg target, where the Company has identified a shallow-dipping, near-surface mineralised pegmatite body with true thickness up to 35m, which contributed 890,892 tonnes of the Resource increase to 36.8Mt at 1.24% Li2O.
- Potential to grow the Resource further; step-out drilling planned at five priority deposits and one new exploration target identified for initial reverse circulation ("RC") evaluation.
Commenting, Neil Herbert, Executive Chairman of Atlantic Lithium, said:
"We are pleased to report an increase in the Mineral Resource for the Ewoyaa Lithium Project to 36.8Mt at 1.24% Li2O, which reaffirms Ewoyaa's status as one of the leading hard rock lithium projects.
"The increase follows the limited drilling programme completed recently, which was focused on supporting our mine planning activities rather than expanding the resource base, but through which we identified the Dog-Leg target, which has added near-surface tonnes to the Ewoyaa Resource. We are pleased to see this lucky strike at Dog-Leg contributing an additional circa 891,000 tonnes to the enlarged 36.8Mt at 1.24% Li2O Resource.
"While our current focus remains firmly on advancing Ewoyaa towards shovel-readiness, we recognise the significant potential across our exploration portfolio to increase the Resource further."
Figures and Tables referred to in this release can be viewed in the PDF version available via this link:
http://www.rns-pdf.londonstockexchange.com/rns/3567Y_1-2024-7-30.pdf
Mineral Resource Estimate Upgrade
An upgraded MRE of 36.8Mt at 1.24% Li2O was completed for the Ewoyaa deposit and surrounding pegmatites; collectively termed the "Ewoyaa Lithium Project".
The MRE increase follows a targeted drilling programme aimed at supporting the mine build activities at the Project. This comprised sterilisation drilling to support the plant and haul road design and resource conversion drilling, aimed at converting Inferred resources to Indicated and Measured, to provide mine plan optionality. The drilling programme resulted in the combined Measured and Indicated resource increasing to 81% of the Total Mineral Resource (to 29.8 Mt at 1.26% Li2O).
During drilling programme, the Dog-Leg target was identified, with prioritised drilling subsequently undertaken, which returned multiple broad and high-grade intersections, from which the Company has identified a shallow-dipping, near-surface mineralised pegmatite body with true thickness up to 35m. The Dog-Leg target contributed 890,892 tonnes, comprising 332,100 tonnes at 1.01% Li2O Indicated and 558,792 tonnes at 1.13% Li2O Inferred, of the increase in resources to 36.8Mt at 1.24% Li2O.
The Mineral Resource is based on 168,015m of drilling completed at the Project to date, inclusive of infill and extensional drilling undertaken since the February 2023 MRE reported by the Company, comprising 148,865m of reverse circulation ("RC"), 12,639m of diamond core ("DD"), 5,311m of reverse circulation with diamond tail ("RCD") and 1,200m of reverse circulation hydrology holes ("RCH").
The MRE includes a total of 3.7Mt at 1.37% Li2O in the Measured category, 26.1Mt at 1.24% Li2O in the Indicated category and 7.0Mt at 1.15% Li2O in the Inferred category (refer Table 1). The independent MRE for Ewoyaa was completed by Ashmore Advisory Pty Ltd ("
Table 1: Ewoyaa Mineral Resource Estimate (0.5% Li2O Cut-off)
|
Measured Mineral Resource |
||||
Type |
Tonnage |
Li2O |
Cont. Lithium Oxide |
||
|
Mt |
% |
kt |
||
Primary |
3.7 |
1.37 |
51 |
||
Total |
3.7 |
1.37 |
51 |
||
|
|
|
|
||
|
Indicated Mineral Resource |
||||
Type |
Tonnage |
Li2O |
Cont. Lithium Oxide |
||
|
Mt |
% |
kt |
||
Weathered |
0.5 |
1.08 |
5 |
||
Primary |
25.6 |
1.25 |
319 |
||
Total |
26.1 |
1.24 |
324 |
||
|
|
|
|
||
|
Inferred Mineral Resource |
||||
Type |
Tonnage |
Li2O |
Cont. Lithium Oxide |
||
|
Mt |
% |
kt |
||
Weathered |
1.8 |
1.12 |
20 |
||
Primary |
5.2 |
1.16 |
60 |
||
Total |
7.0 |
1.15 |
80 |
||
|
|
|
|
||
|
Total Mineral Resource |
||||
Type |
Tonnage |
Li2O |
Cont. Lithium Oxide |
||
|
Mt |
% |
kt |
||
Weathered |
2.3 |
1.11 |
25 |
||
Primary |
34.5 |
1.25 |
430 |
||
Total |
36.8 |
1.24 |
455 |
||
Note: The Mineral Resource has been compiled under the supervision of Mr. Shaun Searle who is a director of Ashmore Advisory Pty Ltd and a Registered Member of the Australian Institute of Geoscientists. Mr. Searle has sufficient experience that is relevant to the style of mineralisation and type of deposit under consideration and to the activity that he has undertaken to qualify as a Competent Person as defined in the JORC Code.
All Mineral Resources figures reported in the table above represent estimates at June 2024. Mineral Resource estimates are not precise calculations, being dependent on the interpretation of limited information on the location, shape and continuity of the occurrence and on the available sampling results. The totals contained in the above table have been rounded to reflect the relative uncertainty of the estimate. Rounding may cause some computational discrepancies.
Mineral Resources are reported in accordance with the Australasian Code for Reporting of Exploration Results, Mineral Resources and Ore Reserves (The Joint Ore Reserves Committee Code - JORC 2012 Edition).
Table 2 below details the history of Mineral Resource Estimates reported by the Company for the Ewoyaa Lithium Project to date, inclusive of the MRE increase reported in this announcement.
Table 2: Ewoyaa Mineral Resource Estimates Reported to Date
Date |
Classification |
Tonnage |
Li2O |
January 2020 |
Indicated Mineral Resource |
4.5 Mt |
1.39 |
Inferred Mineral Resource |
10.0 Mt |
1.27 |
|
Total Mineral Resource |
14.5 Mt |
1.31 |
|
December 2021 |
Indicated Mineral Resource |
5.2 Mt |
1.39 |
Inferred Mineral Resource |
16.1 Mt |
1.28 |
|
Total Mineral Resource |
21.3 Mt |
1.31 |
|
March 2022 |
Indicated Mineral Resource |
20.5 Mt |
1.29 |
Inferred Mineral Resource |
9.6 Mt |
1.19 |
|
Total Mineral Resource |
30.1 Mt |
1.26 |
|
February 2023 |
Measured Mineral Resource |
3.5 Mt |
1.37 |
Indicated Mineral Resource |
24.5 Mt |
1.25 |
|
Inferred Mineral Resource |
7.4 Mt |
1.16 |
|
Total Mineral Resource |
35.3 Mt |
1.25 |
|
July 2024 |
Measured Mineral Resource |
3.7 Mt |
1.37 |
Indicated Mineral Resource |
26.1 Mt |
1.24 |
|
Inferred Mineral Resource |
7.0 Mt |
1.15 |
|
Total Mineral Resource |
36.8 Mt |
1.24 |
There are four main geometallurgical domains at the Project (Primary P1 and P2 and their weathered subsets). Their relative abundances, metallurgical recoveries and concentrate grades are shown in Table 3. The tonnage and grade distribution throughout the entire deposit is illustrated graphically in Figure 1, where a mining bench breakdown using a 10m bench height has been used. The grade tonnage curve for the Ewoyaa Lithium Project Mineral Resource is shown in Figure 2.
Table 3: Material Types, Recoveries and Concentrate Grades (recoveries based on laboratory results)
|
Weathered |
||||
Geomet Type |
Tonnage |
Li2O |
Cont. Lithium |
Recovery |
Conc. Grade |
|
Mt |
% |
kt |
% |
Li2O (%) |
P1 |
2.1 |
1.12 |
24 |
68 |
6.0 |
P2 |
0.2 |
1.03 |
2 |
50 |
6.0 |
Total |
2.3 |
1.11 |
25 |
|
|
|
|
|
|
|
|
|
Primary |
||||
Geomet Type |
Tonnage |
Li2O |
Cont. Lithium |
Recovery |
Conc. Grade |
|
Mt |
% |
kt |
% |
Li2O (%) |
P1 |
31.1 |
1.27 |
393 |
70 |
6.0 |
P2 |
3.5 |
1.06 |
37 |
50 |
5.5 |
Total |
34.5 |
1.25 |
430 |
|
|
Note: As per Table 1 above and metallurgical sign off in Competent Persons section at end of report.
Figure 1: Ewoyaa Tonnage and Grade - 10m Bench Elevation
Figure 2: Ewoyaa Grade - Tonnage Curve for Classified Pegmatite Resource
A plan view of the Ewoyaa Lithium Project prospect areas is shown in Figure 3, with a long section shown in Figure 4 and cross-section within the Ewoyaa Main indicated category zone shown in Figure 5.
Figure 3: Ewoyaa Lithium Project prospect location map (all pegmatite zones) - Asan is located approximately 2.2km northeast of Kaampakrom
Figure 4: Long Section Z-Z' of Ewoyaa Main Wireframes and Drilling (View towards 300°; Solid Colours = Resource Wireframes, Wireframe Edges = Pegmatite Wireframes)
Figure 5: Cross Section A-A' of Ewoyaa Wireframes and Drilling
Geology and Geological Interpretation
The Project area lies within the Birimian Supergroup, a Proterozoic volcano-sedimentary basin located in
The Project area has two clearly defined material types of spodumene bearing lithium mineralisation. The Company has termed these material types as Pegmatite Type 1 ("P1") and Pegmatite Type 2 ("P2"). P1 material is characterised by coarse grained spodumene bearing pegmatite which exhibits very coarse to pegmatoidal, euhedral to subhedral spodumene crystals. P2 material consists of medium grained spodumene, euhedral to subhedral in shape and can compose up to 50% of the rock. The two material types have different metallurgical recoveries.
Drill Methods
The database contains data for the drilling conducted by the Company since 2018, with an overview of drill types shown in Figure 6.
Figure 6: Drill Type Location Map
Drilling at the deposit extends to a maximum drill depth of 386m and the mineralisation was modelled from surface to a depth of approximately 380m below surface. The estimate is based on good quality reverse circulation ("RC") and diamond core ("DD") drilling data. Drill hole spacing is as close as 20m by 15m in some portions of the Ewoyaa deposit; then spacing is predominantly 40m by 40m across the Project and up to 80m by 80m in parts of lesser known mineralisation.
The RC drilling used a combination of 5.25' and 5.75', face sampling hammers. The DD used PQ and HQ (resulting in 85mm and 63.5mm diameter core respectively) diameter core barrels. The DD holes were completed from surface with PQ to maximise recovery in weathered zones, with reversion to HQ once ground conditions improved within fresh material.
In 2018, Phase 1 RC holes were completed on a nominal 100m by 50m grid pattern, targeting the Ewoyaa Main mineralised system. Phases 2 to 5 reduced the wide spacing to 80m by 40m and down to 40m by 40m in the well drilled portions of the Project. Phase 5 was a major infill drilling program down to 40m by 40m over most of the Project. Phases 6 and 7 included extensional drilling in areas of open mineralisation, as well as close spaced infill drilling in portions of the Ewoyaa deposit.
A summary of the drilling data within the Ewoyaa Lithium Project Mineral Resource area is shown in Table 4.
Table 4: Summary of Drilling at the Project
Hole Type |
In Database |
In Mineral Resource |
|||
Drill holes |
Drill holes |
Intersection |
|||
Number |
Metres |
Number |
Metres |
Metres |
|
RCH |
12 |
1,200 |
|
|
|
RC |
1,048 |
148,865 |
722 |
106,609 |
19,580 |
RCD |
36 |
5,311 |
33 |
4,881 |
786 |
DD |
109 |
12,639 |
101 |
11,558 |
5,393 |
Total |
1,205 |
168,015 |
856 |
123,048 |
25,759 |
Sampling Methodology
During Phase 1 and 2, RC drilling bulk samples and splits were collected at the rig for every metre interval drilled, the splits being undertaken using a riffle splitter. Since Phase 3, RC samples were split with a rig mounted cone spitter which took duplicate samples for quality control purposes.
Diamond core was cut with a core saw and selected half core samples totalling 2,131.1kg were dispatched to Nagrom Laboratory in
Selected core intervals were cut to quarter core with a saw at one metre intervals or to geological contacts; and since December 2018 were sent to Intertek Laboratory in Tarkwa for sample preparation. Prior to that, samples were sent to SGS Laboratory in Tarkwa for sample preparation.
Sample Preparation
Since December 2018, samples were submitted to Intertek Tarkwa (SP02/SP12) for sample preparation. Samples were weighed, dried and crushed to -2mm in a Boyd crusher with an 800-1,200g rotary split, producing a nominal 1,500g split crushed sample; which was subsequently pulverised in a LM2 ring mill. Samples were pulverised to a nominal 85% passing 75µm. All the preparation equipment was flushed with barren material prior to the commencement of the job. Coarse reject material was kept in the original bag. Lab sizing analysis was undertaken on a nominal 1:25 basis. Final pulverised samples (20g) were airfreighted to Intertek in
Prior to December 2018, all Phase 1 samples were submitted to SGS Tarkwa for preparation (PRP100) and subsequently forwarded to SGS Johannesburg and later SGS Vancouver for analysis (ICP90A).
Sample Analysis Method
Since December 2018, samples were sent to Intertek Laboratory in
Prior to December 2018, Phase 1 samples were submitted to SGS Johannesburg and later SGS Vancouver for analysis (ICP90A). ICP90 is a 28 element combination Na2O2 fusion with ICP-OES. ICP-MS was added to some submissions for additional trace element characterisation purposes.
All phase 1 SGS pulps were subsequently sent to Intertek Laboratory Perth for re-analysis (FP6/MS/OES) and included in the resource estimate.
Mineral Resource Classification
The Project deposits show good continuity of the main mineralised units which allowed the drill hole intersections to be modelled into coherent, geologically robust domains. Consistency is evident in the thickness of the structure, and the distribution of grade appears to be reasonable along and across strike.
The Mineral Resource was classified as Measured, Indicated and Inferred Mineral Resource based on data quality, sample spacing, and lode continuity. The Measured Mineral Resource was confined to fresh rock within areas drilled at 20m by 15m along with robust continuity of geology and Li2O grade. The Indicated Mineral Resource was defined within areas of close spaced drilling of less than 40m by 40m, and where the continuity and predictability of the lode positions was good. In addition, Indicated Mineral Resource was classified in weathered rock overlying fresh Measured Mineral Resource. The Inferred Mineral Resource was assigned to transitional material, areas where drill hole spacing was greater than 40m by 40m, where small, isolated pods of mineralisation occur outside the main mineralised zones, and to geologically complex zones.
The block model has an attribute "class" for all blocks within the mineralisation wireframes coded as either "mes" for Measured, "ind" for Indicated "inf" for Inferred. The Mineral Resource classification is shown in Figure 7 and Figure 8.
Figure 7: Mineral Resource Classification Plan View
Figure 8: Mineral Resource Classification Oblique View - Ewoyaa Main (Facing NE)
The extrapolation of the lodes along strike and down-dip have been limited to distances of 40m. Zones of extrapolation are classified as Inferred Mineral Resource.
The JORC Code (2012) describes a number of criteria which must be addressed in the documentation of Mineral Resource estimates prior to public release of the information. The criteria provide a means of assessing whether or not parts of or the entire data inventory used in the estimate are adequate for that purpose. The Mineral Resources stated in this document are based on the criteria set out in Table 1 of that Code. These criteria are listed in Appendix 1 and Appendix 2.
Cut-off Grade
The Statement of Mineral Resources has been constrained by the mineralisation solids, reported above a cut-off grade of 0.5% Li2O. Whittle optimisations demonstrate reasonable prospects for eventual economic extraction.
Estimation Methodology
A Surpac block model was created to encompass the extents of the known mineralisation, including an additional block model for the Asan prospect. The block model was rotated on a bearing of 30°, with block dimensions of 10m NS by 10m EW by 5m vertical with sub-cells of 2.5m by 2.5m by 1.25m. The block model was estimated using Ordinary Kriging ("OK") grade interpolation. The mineralisation was constrained by pegmatite geology wireframes and internal lithium bearing mineralisation wireframes prepared using a nominal 0.4% Li2O cut-off grade and a minimum down-hole length of 3m. The wireframes were used as hard boundaries for the interpolation.
Bulk densities ranging between 1.7t/m3 and 2.78t/m3 were assigned in the block model dependent on lithology, mineralisation and weathering. These densities were applied based on 14,046 bulk density measurements conducted by the Company on 101 DD holes and 35 RC holes with diamond tails conducted across the breadth of the Project. The measurements were separated using weathering surfaces, geology and mineralisation solids, with averages assigned in the block model.
Mining and Metallurgical Methods and Parameters
It is assumed that the Ewoyaa Project can be mined with open pit mining techniques. Preliminary metallurgical test work indicates that there are four main geometallurgical domains; weathered and fresh coarse grained spodumene bearing pegmatite (P1); and weathered and fresh medium grained spodumene bearing pegmatite (P2). From test work completed to date at a 6.3mm crush, the P1 material produces a 6% Li2O concentrate at approximately 70 to 85% recovery (average 75% recovery), whilst P2 material produces 5.5 to 6% Li2O concentrate at approximately 35 to 65% recovery (average 47% recovery).
JORC Table 1, Section 1 (Sampling Techniques and Data) and Section 2 (Reporting of Exploration Results) are included in Appendix 1.
JORC Table 1, Section 3 (Estimation and Reporting of Mineral Resources) is included in Appendix 2.
End Note
1 Ore Reserves, Mineral Resources and Production Targets
The information in this announcement that relates to Ore Reserves, Mineral Resources and Production Targets complies with the 2012 Edition of the Australasian Code for Reporting of Exploration Results, Mineral Resources and Ore Reserves (JORC Code). The Company is not aware of any new information or data that materially affects the information included in this announcement, the Ewoyaa Lithium Project Definitive Feasibility Study announcement, dated 29 June 2023 (in which the Company reported Ore Reserves and Production Targets in respect of the Project), or the Grant of the Ewoyaa Mining Lease announcement, dated 20 October 2023 (in which the Company reported the revision of material assumptions for the Project). This announcement and the announcements dated 29 June 2023 and 20 October 2023 are available at www.atlanticlithium.com.au.
2 Ewoyaa to become one of the largest spodumene concentrate producers globally - Based on a comparison of targeted spodumene concentrate production capacity (ktpa, 100% basis) of select hard rock spodumene projects globally (refer Company presentation dated 8 September 2023).
Competent Persons
Information in this announcement relating to the exploration results is based on data reviewed by Mr I. Iwan Williams (BSc. Hons Geology), General Manager - Exploration of the Company. Mr Williams is a Member of the Australian Institute of Geoscientists (#9088) who has in excess of 30 years' experience in mineral exploration and is a Qualified Person under the AIM Rules. Mr Williams consents to the inclusion of the information in the form and context in which it appears.
Information in this announcement relating to Mineral Resources was compiled by Shaun Searle, a Member of the Australian Institute of Geoscientists. Mr Searle has sufficient experience that is relevant to the style of mineralisation and type of deposit under consideration and to the activity being undertaken to qualify as a Competent Person as defined in the 2012 Edition of the 'Australasian Code for Reporting of Exploration Results, Mineral Resources and Ore Reserves' and is a Qualified Person under the AIM Rules. Mr Searle is a director of
This announcement contains inside information for the purposes of Article 7 of the Market Abuse Regulation (EU) 596/2014 as it forms part of
For any further information, please contact:
Atlantic Lithium Limited
Neil Herbert (Executive Chairman)
Amanda Harsas (Finance Director and Company Secretary)
|
www.atlanticlithium.com.au |
|||
|
IR@atlanticlithium.com.au |
|||
|
Tel: +61 2 8072 0640 |
|||
SP Angel Corporate Finance LLP Nominated Adviser Jeff Keating Charlie Bouverat Tel: +44 (0)20 3470 0470 |
Yellow Jersey PR Limited Charles Goodwin Bessie Elliot Tel: +44 (0)20 3004 9512
|
Canaccord Genuity Limited Financial Adviser: Raj Khatri ( Duncan
Corporate Broking: James Asensio Tel: +44 (0) 20 7523 4500 |
|
|
Notes to Editors:
About Atlantic Lithium
Atlantic Lithium is an AIM, ASX, GSE and OTCQX-listed lithium company advancing its flagship project, the Ewoyaa Lithium Project, a significant lithium spodumene pegmatite discovery in
The Definitive Feasibility Study for the Project indicates the production of 3.6Mt of spodumene concentrate over a 12-year mine life, making it one of the largest spodumene concentrate mines in the world.
The Project, which was awarded a Mining Lease in October 2023, is being developed under an earn-in agreement with Piedmont Lithium Inc.
Atlantic Lithium holds a portfolio of lithium projects within 509km2 and 774km2 of granted and under-application tenure across
APPENDIX 1
JORC Table 1, Section 1 - Sampling Techniques and Data
Criteria |
JORC Code Explanation |
Commentary |
Sampling techniques |
· Nature and quality of sampling (e.g. cut channels, random chips, or specific specialised industry standard measurement tools appropriate to the minerals under investigation, such as down hole gamma sondes, or handheld XRF instruments, etc). These examples should not be taken as limiting the broad meaning of sampling. · Include reference to measures taken to ensure sample representivity and the appropriate calibration of any measurement tools or systems used. · Aspects of the determination of mineralisation that are Material to the Public Report. In cases where 'industry standard' work has been done this would be relatively simple (eg 'reverse circulation drilling was used to obtain 1 m samples from which 3 kg was pulverised to produce a 30 g charge for fire assay'). In other cases more explanation may be required, such as where there is coarse gold that has inherent sampling problems. Unusual commodities or mineralisation types (eg submarine nodules) may warrant disclosure of detailed information. |
· RC drill holes were routinely sampled at 1m intervals with a nominal 3-6kg sub-sample split off for assay using a rig-mounted cone splitter at 1m intervals. · DD holes were quarter core sampled at 1m intervals or to geological contacts for geochemical analysis. · For assaying, splits from all prospective ore zones (i.e. logged pegmatites +/- interburden) were sent for assay. Outside of these zones, the splits were composited to 4m using a portable riffle splitter. · Holes without pegmatite were not assayed. · Approximately 5% of all samples submitted were standards and coarse blanks. Blanks were typically inserted with the interpreted ore zones after the drilling was completed. · Approximately 2.5% of samples submitted were duplicate samples collected after logging using a riffle splitter or as a second split using the rig mounted cone splitter at 1 m interval and sent to an umpire laboratory. This ensured zones of interest were duplicated and not missed during alternative routine splitting of the primary sample. · Prior to the December 2018 - SGS Tarkwa was used for sample preparation (PRP100) and subsequently forwarded to SGS Johannesburg for analysis; and later SGS Vancouver for analysis (ICP90A). · Post December 2018 to present - Intertek Tarkwa was used for sample preparation (SP02/SP12) and subsequently forwarded to Intertek Perth for analysis (FP6/MS/OES - 21 element combination Na2O2 fusion with combination OES/MS), and also (4A/OM) for Na. · ALS Laboratory in |
Drilling techniques |
· Drill type (eg core, reverse circulation, open-hole hammer, rotary air blast, auger, Bangka, sonic, etc) and details (eg core diameter, triple or standard tube, depth of diamond tails, face-sampling bit or other type, whether core is oriented and if so, by what method, etc).
|
· Seven phases of drilling were undertaken at the Project using RC and DD techniques. All the RC drilling used face sampling hammers. · Phase 1 and 2 programs used a 5.25 inch hammers while Phase 3 used a 5.75-inch hammer. Phase 4 through 7 used 5.5 inch · All DD holes were completed using PQ and HQ core from surface (85mm and 63.5mm). · All DD holes were drilled in conjunction with a Reflex ACT II tool; to provide an accurate determination of the bottom-of-hole orientation. · All fresh core was orientated to allow for geological, structural and geotechnical logging by a Company geologist. |
Drill sample recovery |
· Method of recording and assessing core and chip sample recoveries and results assessed. · Measures taken to maximise sample recovery and ensure representative nature of the samples. · Whether a relationship exists between sample recovery and grade and whether sample bias may have occurred due to preferential loss/gain of fine/coarse material. |
· A semi-quantitative estimate of sample recovery was completed for the vast majority of drilling. This involved weighing both the bulk samples and splits and calculating theoretical recoveries using assumed densities. Where samples were not weighed, qualitative descriptions of the sample size were recorded. Some sample loss was recorded in the collaring of the RC drill holes. · DD recoveries were measured and recorded. Recoveries in excess of 95.8% have been achieved for the DD drilling program. Drill sample recovery and quality is adequate for the drilling technique employed. · The DD twin program has identified a positive grade bias for iron in the RC compared to the DD results. |
Logging |
· Whether core and chip samples have been geologically and geotechnically logged to a level of detail to support appropriate Mineral Resource estimation, mining studies and metallurgical studies. · Whether logging is qualitative or quantitative in nature. Core (or costean, channel, etc) photography. · The total length and percentage of the relevant intersections logged. |
· All drill sample intervals were geologically logged by Company geologists. · Where appropriate, geological logging recorded the abundance of specific minerals, rock types and weathering using a standardised logging system that captured preliminary metallurgical domains. · All logging is qualitative, except for the systematic collection of magnetic susceptibility data which could be considered semi quantitative. · Strip logs have been generated for each drill hole to cross-check geochemical data with geological logging. · A small sample of washed RC drill material was retained in chip trays for future reference and validation of geological logging, and sample reject materials from the laboratory are stored at the Company's field office. · All drill holes have been logged and reviewed by Company technical staff. · The logging is of sufficient detail to support the current reporting of a Mineral Resource. |
Sub-sampling techniques and sample preparation |
· If core, whether cut or sawn and whether quarter, half or all core taken. · If non-core, whether riffled, tube sampled, rotary split, etc and whether sampled wet or dry. · For all sample types, the nature, quality and appropriateness of the sample preparation technique. · Quality control procedures adopted for all sub-sampling stages to maximise representivity of samples. · Measures taken to ensure that the sampling is representative of the in situ material collected, including for instance results for field duplicate/second-half sampling. · Whether sample sizes are appropriate to the grain size of the material being sampled. |
· RC samples were cone split at the drill rig. For interpreted waste zones the 1 or 2m rig splits were later composited using a riffle splitter into 4m composite samples. · DD core was cut with a core saw and selected half core samples dispatched to Nagrom Laboratory in · The other half of the core, including the bottom-of-hole orientation line, was retained for geological reference. · The remaining DD core was quarter cored for geochemical analysis. · Since December 2018, samples were submitted to Intertek Tarkwa (SP02/SP12) for sample preparation. Samples were weighed, dried and crushed to -2mm in a Boyd crusher with an 800-1,200g rotary split, producing a nominal 1,500g split crushed sample; which was subsequently pulverised in a LM2 ring mill. Samples were pulverised to a nominal 85% passing 75µm. All the preparation equipment was flushed with barren material prior to the commencement of the job. Coarse reject material was kept in the original bag. Lab sizing analysis was undertaken on a nominal 1:25 basis. Final pulverised samples (20g) were airfreighted to Intertek in · The vast majority of samples were drilled dry. Moisture content was logged qualitatively. All intersections of the water table were recorded in the database. · Field sample duplicates were taken to evaluate whether samples were representative and understand repeatability, with good repeatability. · Sample sizes and laboratory preparation techniques were appropriate and industry standard. |
Quality of assay data and laboratory tests |
· The nature, quality and appropriateness of the assaying and laboratory procedures used and whether the technique is considered partial or total. · For geophysical tools, spectrometers, handheld XRF instruments, etc, the parameters used in determining the analysis including instrument make and model, reading times, calibrations factors applied and their derivation, etc. · Nature of quality control procedures adopted (eg standards, blanks, duplicates, external laboratory checks) and whether acceptable levels of accuracy (ie lack of bias) and precision have been established. |
· Analysis for lithium and a suite of other elements for Phase 1 drilling was undertaken at SGS Johannesburg / · Review of standards and blanks from the initial submission to · Results of analyses for field sample duplicates are consistent with the style of mineralisation and considered to be representative. Internal laboratory QAQC checks are reported by the laboratory, including sizing analysis to monitor preparation and internal laboratory QA/QC. These were reviewed and retained in the company drill hole database. · 155 samples were sent to an umpire laboratory (ALS) and/assayed using equivalent techniques, with results demonstrating good repeatability. · Atlantic Lithium's review of QAQC suggests Intertek Perth laboratories performed within acceptable limits. · No geophysical methods or hand-held XRF units have been used for determination of grades in the Mineral Resource. |
Verification of sampling and assaying |
· The verification of significant intersections by either independent or alternative company personnel. · The use of twinned holes. · Documentation of primary data, data entry procedures, data verification, data storage (physical and electronic) protocols. · Discuss any adjustment to assay data. |
· Significant intersections were visually field verified by company geologists and Shaun Searle of · Drill hole data was compiled and digitally captured by Company geologists in the field. Where hand-written information was recorded, all hardcopy records were kept and archived after digitising. · Phase 1 and 2 drilling programs were captured on paper or locked excel templates and migrated to an MS Access database and then into Datashed (industry standard drill hole database management software). The Phase 3 to 6 programs were captured using LogChief which has inbuilt data validation protocols. All analytical results were transferred digitally and loaded into the database by a Datashed consultant. · The data was audited, and any discrepancies checked by the Company personnel before being updated in the database. · Twin DD holes were drilled to verify results of the RC drilling programs. Results indicate that there is iron contamination in the RC drilling process. · Reported drill hole intercepts were compiled by the Chief Geologist. · Adjustments to the original assay data included converting Li ppm to Li2O%. |
Location of data points |
· Accuracy and quality of surveys used to locate drill holes (collar and down-hole surveys), trenches, mine workings and other locations used in Mineral Resource estimation. · Specification of the grid system used. · Quality and adequacy of topographic control. |
· The collar locations were surveyed in WGS84 Zone 30 North using DGPS survey equipment, which is accurate to 0.11mm in both horizontal and vertical directions. All holes were surveyed by qualified surveyors. Once validated, the survey data was uploaded into Datashed. · RC drill holes were routinely down hole surveyed every 6m using a combination of EZ TRAC 1.5 (single shot) and Reflex Gyroscopic tools. · After the tenth drill hole, the survey method was changed to Reflex Gyro survey with 6m down hole data points measured during an end-of-hole survey. · All Phase 2 and 3 drill holes were surveyed initially using the Reflex Gyro tool, but later using the more efficient Reflex SPRINT tool. Phases 4 through 7 drill holes were surveyed using a Reflex SPRINT tool. · LiDAR survey Southern Mapping to produce rectified colour images and a digital terrain model (DTM) 32km2, Aircraft C206 aircraft-mounted LiDAR Riegl Q780 Camera Hasselblad H5Dc with 50mm Fixfocus lens. · Coordinate system: WGS84 UTM30N with accuracy to ±0.04. · The topographic survey and photo mosaic output from the survey is accurate to 20mm. In addition, local site survey data was used to generate the topographic surface for the Asan area. · Locational accuracy at collar and down the drill hole is considered appropriate for resource estimation purposes. |
Data spacing and distribution |
· Data spacing for reporting of Exploration Results. · Whether the data spacing and distribution is sufficient to establish the degree of geological and grade continuity appropriate for the Mineral Resource and Ore Reserve estimation procedure(s) and classifications applied. · Whether sample compositing has been applied. |
· The RC holes were initially drilled on 100m spaced sections and 50m hole spacings orientated at 300° or 330° with dips ranging from -50° to -60°. Planned hole orientations/dips were occasionally adjusted due to pad and/or access constraints. · Hole spacing was reduced to predominantly 40m spaced sections and 40m hole spacings, with infill to 20m by 15m in the upper portions of the Ewoyaa Main deposit. Holes are generally angled perpendicular to interpreted mineralisation orientations at the Project. · Samples were composited to 1m intervals prior to estimation. |
Orientation of data in relation to geological structure |
· Whether the orientation of sampling achieves unbiased sampling of possible structures and the extent to which this is known, considering the deposit type. · If the relationship between the drilling orientation and the orientation of key mineralised structures is considered to have introduced a sampling bias, this should be assessed and reported if material. |
· The drill line and drill hole orientation are oriented as close as practicable to perpendicular to the orientation of the general mineralised orientation. · Most of the drilling intersects the mineralisation at close to 90 degrees ensuring intersections are representative of true widths. It is possible that new geological interpretations and/or infill drilling requirements may result in changes to drill orientations on future programs. · No orientation based sampling bias has been identified in the data. |
Sample security |
· The measures taken to ensure sample security. |
· Samples were stored on site prior to road transportation by Company personnel to the SGS preparation laboratory. · With the change of laboratory to Intertek, samples were picked up by the contractor and transported to the sample preparation facility in Tarkwa. |
Audits or reviews |
· The results of any audits or reviews of sampling techniques and data. |
· Prior to the drilling program, a third-party Project review was completed by an independent consultant experienced with the style of mineralisation. · In addition, Shaun Searle of |
JORC Table 1, Section 2 - Reporting of Exploration Results
Criteria |
JORC Code Explanation |
Commentary |
Mineral tenement and land tenure status |
· Type, reference name/number, location and ownership including agreements or material issues with third parties such as joint ventures, partnerships, overriding royalties, native title interests, historical sites, wilderness or national park and environmental settings. · The security of the tenure held at the time of reporting along with any known impediments to obtaining a license to operate in the area. |
· The Project cover two contiguous licences the Mankessim (RL 3/55) and Mankessim South (PL.3/109) licence. · The Ministry of Lands and Natural Resources granted a Mining Lease to Barari DV Ghana Ltd. for the Ewoyaa Lithium Project on 19th October 2023, extending over an area of 42.63 km2 or 203 cadastral blocks and valid for an initial 15-year renewable period. · The Ewoyaa Lithium Project includes mineral resources defined within the original Mankessim South PL, and as a consequence 28 cadastral blocks were transferred from Green Metals Resources' PL.3/109 to Barari DV Ghana's RL.3/55 and were incorporated into the Ewoyaa Lithium Project Mining Lease, thus reducing the Mankessim South PL size from 62 cadastral blocks to 34 cadastral blocks. |
Exploration done by other parties |
· Acknowledgment and appraisal of exploration by other parties. |
· Historical trenching and mapping were completed by the Ghana Geological survey during the 1960's. But for some poorly referenced historical maps, none of the technical data from this work was located. Many of the historical trenches were located, cleaned and re-logged. No historical drilling was completed. |
Geology |
· Deposit type, geological setting and style of mineralisation. |
· Pegmatite-hosted lithium deposits are the target for exploration. This style of mineralisation typically forms as dykes and sills intruding or in proximity to granite source rocks. · Surface geology within the Project area typically consists of sequences of mica, staurolite and garnet-bearing pelitic schist and granite with lesser pegmatite and mafic intrusives. Outcrops are typically sparse and confined to ridge tops with colluvium and mottled laterite blanketing much of the undulating terrain making geological mapping challenging. The hills are often separated by broad, sandy drainages. |
Drill hole information |
· A summary of all information material to the under-standing of the exploration results including a tabulation of the following information for all Material drill holes: · easting and northing of the drill hole collar · elevation or RL (Reduced Level - elevation above sea level in metres) of the drill hole collar · dip and azimuth of the hole · down hole length and interception depth · hole length · If the exclusion of this information is justified on the basis that the information is not Material and this exclusion does not detract from the understanding of the report, the Competent Person should clearly explain why this is the case. |
· Exploration results are not being reported. · All information has been included in the appendices. No drill hole information has been excluded. |
Data aggregation methods |
· In reporting Exploration Results, weighting averaging techniques, maximum and/or minimum grade truncations (e.g. cutting of high grades) and cut-off grades are usually Material and should be stated. · Where aggregate intercepts incorporate short lengths of high grade results and longer lengths of low grade results, the procedure used for such aggregation should be stated and some typical examples of such aggregations should be shown in detail. · The assumptions used for any reporting of metal equivalent values should be clearly stated. |
· Exploration results are not being reported. · Not applicable as a Mineral Resource is being reported. · No metal equivalent values are being reported. |
Relationship between mineralisation widths and intercept lengths |
· These relationships are particularly important in the reporting of Exploration Results. · If the geometry of the mineralisation with respect to the drill hole angle is known, its nature should be reported. · If it is not known and only the down hole lengths are reported, there should be a clear statement to this effect (e.g. 'down hole length, true width not known'). |
· The drill line and drill hole orientation are oriented as close to 90° degrees to the orientation of the anticipated mineralised orientation as practicable. · The majority of the drilling intersects the mineralisation between 60° and 80° degrees. |
Diagrams |
· Appropriate maps and sections (with scales) and tabulations of intercepts should be included for any significant discovery being reported. These should include, but not be limited to a plan view of drill hole collar locations and appropriate sectional views. |
· Relevant diagrams have been included within the Mineral Resource report main body of text. |
Balanced Reporting |
· Accuracy and quality of surveys used to locate drill holes (collar and down-hole surveys), trenches, mine workings and other locations used in Mineral Resource estimation. · Where comprehensive reporting of all Exploration Results is not practicable, representative reporting of both low and high grades and/or widths should be practiced to avoid misleading reporting of Exploration Results. |
· All hole collars were surveyed WGS84 Zone 30 North grid using a differential GPS. All RC and DD holes were down-hole surveyed with a north-seeking gyroscopic tool. · Exploration results are not being reported. |
Other substantive exploration data |
· Other exploration data, if meaningful and material, should be reported including (but not limited to): geological observations; geophysical survey results; geochemical survey results; bulk samples - size and method of treatment; metallurgical test results; bulk density, groundwater, geotechnical and rock characteristics; potential deleterious or contaminating substances. |
· Results were estimated from drill hole assay data, with geological logging used to aid interpretation of mineralised contact positions. · Geological observations are included in the report. |
Further work |
· The nature and scale of planned further work (e.g. tests for lateral extensions or depth extensions or large- scale step-out drilling). · Diagrams clearly highlighting the areas of possible extensions, including the main geological interpretations and future drilling areas, provided this information is not commercially sensitive. |
· Follow up RC and DD drilling may be undertaken. · Further metallurgical test work may be required as the Project progresses through the study stages. · Drill spacing is currently considered adequate for the current level of interrogation of the Project. |
APPENDIX 2
JORC Table 1, Section 3 - Estimation and Reporting of Mineral Resources
Criteria |
JORC Code Explanation |
Commentary |
|||||||||||||||||||||||||||||||||||||||||||||||||||||||||||||||||
Database integrity |
· Measures taken to ensure that data has not been corrupted by, for example, transcription or keying errors, between its initial collection and its use for Mineral Resource estimation purposes. · Data validation procedures used. |
· The database has been systematically audited by Atlantic Lithium geologists. · All drilling data has been verified as part of a continuous validation procedure. Once a drill hole is imported into the database a report of the collar, down-hole survey, geology, and assay data are produced. This is then checked by an Atlantic Lithium geologist and any corrections are completed by the database manager. |
|||||||||||||||||||||||||||||||||||||||||||||||||||||||||||||||||
Site visits |
· Comment on any site visits undertaken by the Competent Person and the outcome of those visits. · If no site visits have been undertaken indicate why this is the case. |
· A site visit was conducted by Shaun Searle of |
|||||||||||||||||||||||||||||||||||||||||||||||||||||||||||||||||
Geological interpretation |
· Confidence in (or conversely, the uncertainty of) the geological interpretation of the mineral deposit. · Nature of the data used and of any assumptions made. · The effect, if any, of alternative interpretations on Mineral Resource estimation. · The use of geology in guiding and controlling Mineral Resource estimation. · The factors affecting continuity both of grade and geology. |
· The confidence in the geological interpretation is considered to be good and is based on visual confirmation in outcrop and within drill hole intersections. · Geochemistry and geological logging have been used to assist identification of lithology and mineralisation. · The Project area lies within the Birimian Supergroup, a Proterozoic volcano-sedimentary basin located in · Infill drilling has supported and refined the model and the current interpretation is considered robust. · Observations from the outcrop of mineralisation and host rocks; as well as infill drilling, confirm the geometry of the mineralisation. · Infill drilling has confirmed geological and grade continuity. |
|||||||||||||||||||||||||||||||||||||||||||||||||||||||||||||||||
Dimensions |
· The extent and variability of the Mineral Resource expressed as length (along strike or otherwise), plan width, and depth below surface to the upper and lower limits of the Mineral Resource. |
· The Project Mineral Resource area extends over a north-south strike length of 4,390m (from 577,380mN - 581,770mN), and includes the 360m vertical interval from 80mRL to -280mRL. |
|||||||||||||||||||||||||||||||||||||||||||||||||||||||||||||||||
Estimation and modelling techniques |
· The nature and appropriateness of the estimation technique(s) applied and key assumptions, including treatment of extreme grade values, domaining, interpolation parameters and maximum distance of extrapolation from data points. If a computer assisted estimation method was chosen include a description of computer software and parameters used. · The availability of check estimates, previous estimates and/or mine production records and whether the Mineral Resource estimate takes appropriate account of such data. · The assumptions made regarding recovery of by-products. · Estimation of deleterious elements or other non-grade variables of economic significance (eg sulphur for acid mine drainage characterisation). · In the case of block model interpolation, the block size in relation to the average sample spacing and the search employed. · Any assumptions behind modelling of selective mining units. · Any assumptions about correlation between variables. · Description of how the geological interpretation was used to control the resource estimates. · Discussion of basis for using or not using grade cutting or capping. · The process of validation, the checking process used, the comparison of model data to drill hole data, and use of reconciliation data if available. |
· Using parameters derived from modelled variograms, Ordinary Kriging ("OK") was used to estimate average block grades in three passes using Surpac software. Linear grade estimation was deemed suitable for the Cape Coast Mineral Resource due to the geological control on mineralisation. The extrapolation of the lodes along strike and down-dip has been limited to a distance of 40m. Zones of extrapolation are classified as Inferred Mineral Resource. · It is assumed that there are no by-products or deleterious elements as shown by metallurgical test work. · Li2O (%), Fe Factored (%), K (%), Mn (%), Na (%) and Ti (ppm) were interpolated into the block model, and subsequently converted to their respective oxide values. · A Surpac block model was created to encompass the extents of the known mineralisation, including an additional block model for the Asan prospect. The block model was rotated on a bearing of 30°, with block dimensions of 10m NS by 10m EW by 5m vertical with sub-cells of 2.5m by 2.5m by 1.25m. The parent block size dimension was selected on the results obtained from Kriging Neighbourhood Analysis and also in consideration of two predominant mineralisation orientations of 30° and 100 to 120°. · An orientated 'ellipsoid' search was used to select data and adjusted to account for the variations in lode orientations, however all other parameters were taken from the variography derived from Domains 1, 2, 3, 4, 7 and 8. Up to three passes were used for each domain. First pass had a range of 50m, with a minimum of 8 samples. For the second pass, the range was extended to 100m, with a minimum of 4 samples. For the third pass, the range was extended to 200m, with a minimum of 1 or 2 samples. A maximum of 16 samples was used for each pass with a maximum of 4 samples per hole. · No assumptions were made on selective mining units. · Correlation analysis was conducted on the domains at Ewoyaa Main. It is evident that Li2O has little correlation with any of the other elements presented in the table. There is a strong correlation between iron and titanium. · The mineralisation was constrained by pegmatite geology wireframes and internal lithium bearing mineralisation wireframes prepared using a nominal 0.4% Li2O cut-off grade and a minimum down-hole length of 3m. The wireframes were used as hard boundaries for the interpolation. · Statistical analysis was carried out on data from 93 mineralised domains. Following a review of the population histograms and log probability plots and noting the low coefficient of variation statistics, it was determined that the application of high grade cuts was not warranted. · Validation of the model included detailed visual validation, comparison of composite grades and block grades by northing and elevation and a nearest neighbour check estimate. Validation plots showed good correlation between the composite grades and the block model grades. |
|||||||||||||||||||||||||||||||||||||||||||||||||||||||||||||||||
Moisture |
· Whether the tonnages are estimated on a dry basis or with natural moisture, and the method of determination of the moisture content. |
· Tonnages and grades were estimated on a dry in situ basis. |
|||||||||||||||||||||||||||||||||||||||||||||||||||||||||||||||||
Cut-off parameters |
· The basis of the adopted cut-off grade(s) or quality parameters applied. |
· The Statement of Mineral Resources has been constrained by the mineralisation solids and reported above a cut-off grade of 0.5% Li2O. Whittle optimisations demonstrate reasonable prospects for eventual economic extraction. Preliminary metallurgical test work indicates that there are four main geometallurgical domains; weathered and fresh coarse grained spodumene bearing pegmatite (P1); and weathered and fresh medium grained spodumene bearing pegmatite (P2). From test work completed to date at a 6.3mm crush, the P1 material produces a 6% Li2O concentrate at approximately 70 to 85% recovery (average 75% recovery), whilst P2 material produces 5.5 to 6% Li2O concentrate at approximately 35 to 65% recovery (average 47% recovery). |
|||||||||||||||||||||||||||||||||||||||||||||||||||||||||||||||||
Mining factors or assumptions |
· Assumptions made regarding possible mining methods, minimum mining dimensions and internal (or, if applicable, external) mining dilution. It is always necessary as part of the process of determining reasonable prospects for eventual economic extraction to consider potential mining methods, but the assumptions made regarding mining methods and parameters when estimating Mineral Resources may not always be rigorous. Where this is the case, this should be reported with an explanation of the basis of the mining assumptions made. |
· · A high level Whittle optimisation of the Mineral Resource supports this view. |
|||||||||||||||||||||||||||||||||||||||||||||||||||||||||||||||||
Metallurgical factors or assumptions |
· The basis for assumptions or predictions regarding metallurgical amenability. It is always necessary as part of the process of determining reasonable prospects for eventual economic extraction to consider potential metallurgical methods, but the assumptions regarding metallurgical treatment processes and parameters made when reporting Mineral Resources may not always be rigorous. Where this is the case, this should be reported with an explanation of the basis of the metallurgical assumptions made. |
· Scoping and PFS level metallurgical test work has been conducted on the Ewoyaa material types. Test work indicates that there are four main geometallurgical material types in occurrence at the Project, with their relative abundances, concentrate grades and recoveries shown below, including a 4% discount factor for bench scale to mine scale efficiencies.
|
|||||||||||||||||||||||||||||||||||||||||||||||||||||||||||||||||
Environmental factors or assumptions |
· Assumptions made regarding possible waste and process residue disposal options. It is always necessary as part of the process of determining reasonable prospects for eventual economic extraction to consider the potential environmental impacts of the mining and processing operation. While at this stage the determination of potential environmental impacts, particularly for a greenfields project, may not always be well advanced, the status of early consideration of these potential environmental impacts should be reported. Where these aspects have not been considered this should be reported with an explanation of the environmental assumptions made. |
· No assumptions have been made regarding environmental factors. The Company will work to mitigate environmental impacts as a result of any future mining or mineral processing. |
|||||||||||||||||||||||||||||||||||||||||||||||||||||||||||||||||
Bulk density |
· Whether assumed or determined. If assumed, the basis for the assumptions. If determined, the method used, whether wet or dry, the frequency of the measurements, the nature, size and representativeness of the samples. · The bulk density for bulk material must have been measured by methods that adequately account for void spaces (vugs, porosity, etc), moisture and differences between rock and alteration zones within the deposit. · Discuss assumptions for bulk density estimates used in the evaluation process of the different materials. |
· Bulk density measurements were completed on selected intervals of diamond core drilled at the deposit. The measurements were conducted at the Cape Coast core processing facility using the water immersion/Archimedes method. The weathered samples were coated in paraffin wax to account for porosity of the weathered samples. · A total of 14,046 measurements were conducted on the Cape Coast mineralisation, with samples obtained from oxide, transitional and fresh material. · Bulk densities ranging between 1.7t/m3 and 2.78t/m3 were assigned in the block model dependent on lithology, mineralisation and weathering. |
|||||||||||||||||||||||||||||||||||||||||||||||||||||||||||||||||
Classification |
· The basis for the classification of the Mineral Resources into varying confidence categories. · Whether appropriate account has been taken of all relevant factors (ie relative confidence in tonnage/grade estimations, reliability of input data, confidence in continuity of geology and metal values, quality, quantity and distribution of the data). · Whether the result appropriately reflects the Competent Person's view of the deposit. |
· The Mineral Resource estimate is reported here in compliance with the 2012 Edition of the 'Australasian Code for Reporting of Exploration Results, Mineral Resources and Ore Reserves' by the Joint Ore Reserves Committee (JORC). The Cape Coast Mineral Resource was classified as Measured, Indicated and Inferred Mineral Resource based on data quality, sample spacing, and lode continuity. The Measured Mineral Resource was confined to fresh rock within areas drilled at 20m by 15m along with robust continuity of geology and Li2O grade. The Indicated Mineral Resource was defined within areas of close spaced drilling of less than 40m by 40m, and where the continuity and predictability of the lode positions was good. In addition, Indicated Mineral Resource was classified in weathered rock overlying fresh Measured Mineral Resource. The Inferred Mineral Resource was assigned to transitional material, areas where drill hole spacing was greater than 40m by 40m, where small, isolated pods of mineralisation occur outside the main mineralised zones, and to geologically complex zones. · The input data is comprehensive in its coverage of the mineralisation and does not favour or misrepresent in-situ mineralisation. The definition of mineralised zones is based on high level geological understanding producing a robust model of mineralised domains. This model has been confirmed by infill drilling which supported the interpretation. Validation of the block model shows good correlation of the input data to the estimated grades. · The Mineral Resource estimate appropriately reflects the view of the Competent Person. |
|||||||||||||||||||||||||||||||||||||||||||||||||||||||||||||||||
Audits or reviews |
· The results of any audits or reviews of Mineral Resource estimates. |
· Internal audits have been completed by |
|||||||||||||||||||||||||||||||||||||||||||||||||||||||||||||||||
Discussion of relative accuracy/ confidence |
· Where appropriate a statement of the relative accuracy and confidence level in the Mineral Resource estimate using an approach or procedure deemed appropriate by the Competent Person. For example, the application of statistical or geostatistical procedures to quantify the relative accuracy of the resource within stated confidence limits, or, if such an approach is not deemed appropriate, a qualitative discussion of the factors that could affect the relative accuracy and confidence of the estimate. · The statement should specify whether it relates to global or local estimates, and, if local, state the relevant tonnages, which should be relevant to technical and economic evaluation. Documentation should include assumptions made and the procedures used. · These statements of relative accuracy and confidence of the estimate should be compared with production data, where available. |
· The geometry and continuity have been adequately interpreted to reflect the applied level of Measured, Indicated and Inferred Mineral Resource. The data quality is good, and the drill holes have detailed logs produced by qualified geologists. A recognised laboratory has been used for all analyses. · The Mineral Resource statement relates to global estimates of tonnes and grade. · No historical mining has occurred; therefore, reconciliation could not be conducted. |
APPENDIX 3
Glossary of Terms and Abbreviations
Assay Measure of valuable mineral content.
Block Model A three-dimensional structure into which parameters are interpolated during the resource estimation process.
Competent Person 'CP' Competent Person, as defined by the JORC Code. A 'Competent Person' is a minerals industry professional who is a Member or Fellow of The Australasian Institute of Mining and Metallurgy, or of the Australian Institute of Geoscientists, or of a 'Recognised Professional Organisation' (RPO), as included in a list available on the JORC and ASX websites. These organisations have enforceable disciplinary processes including the powers to suspend or expel a member. A Competent Person must have a minimum of five years relevant experience in the style of mineralisation or type of deposit under consideration and in the activity which that person is undertaking. If the Competent Person is preparing documentation on Exploration Results, the relevant experience must be in exploration. If the Competent Person is estimating, or supervising the estimation of Mineral Resources, the relevant experience must be in the estimation, assessment and evaluation of Mineral Resources. If the Competent Person is estimating, or supervising the estimation of Ore Reserves, the relevant experience must be in the estimation, assessment, evaluation and economic extraction of Ore Reserves.
Core A solid, cylindrical sample of rock typically produced by a rotating drill bit, but sometimes cut by percussive methods.
Cut-off grade The lowest grade of mineralised material that qualifies as ore in a given deposit; rock of the lowest assay included in an ore estimate.
DD Diamond core drilling.
Deposit An occurrence of economically interesting minerals.
Dip The angle at which a bed, stratum, or vein is inclined from the horizontal, measured perpendicular to the strike and in the vertical plane.
DMS Dense media separation.
Drill hole Technically, a circular hole drilled by forces applied percussively and/or by rotation; loosely and commonly, the name applies to a circular hole drilled in any manner.
Drilling The operation of making deep holes with a drill for prospecting, exploration, or valuation.
Grade The relative quantity or the percentage of ore-mineral or metal content in an orebody.
Exploration The act of investigation for the location of undiscovered mineral deposits.
HQ Diamond drill bit and sample tube size resulting in 96mm diameter hole and 63.5mm diameter core.
ICP-MS Inductively Coupled Plasma-Mass Spectrometry is an analytical technique where samples are ionised using inductively coupled plasma for analysis.
ICP-OES Inductively Coupled Plasma-Optical Emission Spectrometry is an analytical technique where the composition of samples is determined using plasma and spectroscopy.
ICP90A Laboratory analytical method for rock samples where multi-element analysis is undertaken by sodium peroxide fusion with ICP-OES finish.
Indicated Mineral Resource That part of a Mineral Resource for which quantity, grade (or quality), densities, shape and physical characteristics are estimated with sufficient confidence to allow the application of Modifying Factors in sufficient detail to support mine planning and evaluation of the economic viability of the deposit. Geological evidence is derived from adequately detailed and reliable exploration, sampling and testing gathered through appropriate techniques from locations such as outcrops, trenches, pits, workings and drill holes, and is sufficient to assume geological and grade (or quality) continuity between points of observation where data and samples are gathered. An Indicated Mineral Resource has a lower level of confidence than that applying to a Measured Mineral Resource and may only be converted to a Probable Ore Reserve.
Inferred Mineral Resource That part of a Mineral Resource for which quantity and grade (or quality) are estimated on the basis of limited geological evidence and sampling. Geological evidence is sufficient to imply but not verify geological and grade (or quality) continuity. It is based on exploration, sampling and testing information gathered through appropriate techniques from locations such as outcrops, trenches, pits, workings and drill holes. An Inferred Mineral Resource has a lower level of confidence than that applying to an Indicated Mineral Resource and must not be converted to an Ore Reserve. It is reasonably expected that the majority of Inferred Mineral Resources could be upgraded to Indicated Mineral Resources with continued exploration.
JORC Code The Australasian Code for Reporting of Exploration Results, Mineral Resources and Ore Reserves, 2012 Edition, Prepared by the Joint Ore Reserves Committee of The Australasian Institute of Mining and Metallurgy, Australian Institute of Geoscientists and Minerals Council of
LM2 Ring Mill Rock pulverising equipment using vibrating steel bowl containing nested steel rings resulting where crushed rock samples are ground to 85% minus 75 micron in minutes.
Measured Mineral Resource That part of a Mineral Resource for which quantity, grade (or quality), densities, shape, and physical characteristics are estimated with confidence sufficient to allow the application of Modifying Factors to support detailed mine planning and final evaluation of the economic viability of the deposit. Geological evidence is derived from detailed and reliable exploration, sampling and testing gathered through appropriate techniques from locations such as outcrops, trenches, pits, workings and drill holes, and is sufficient to confirm geological and grade (or quality) continuity between points of observation where data and samples are gathered. A Measured Mineral Resource has a higher level of confidence than that applying to either an Indicated Mineral Resource or an Inferred Mineral Resource. It may be converted to a Proved Ore Reserve or under certain circumstances to a Probable Ore Reserve.
Mineral Resource A concentration or occurrence of solid material of economic interest in or on the Earth's crust in such form, grade (or quality), and quantity that there are reasonable prospects for eventual economic extraction. The location, quantity, grade (or quality), continuity and other geological characteristics of a Mineral Resource are known, estimated or interpreted from specific geological evidence and knowledge, including sampling. Mineral Resources are sub-divided, in order of increasing geological confidence, into Inferred, Indicated and Measured categories.
Mineralisation The process by which minerals are introduced into a rock. More generally, a term applied to accumulations of economic or related minerals in quantities ranging from weakly anomalous to economically recoverable.
Modifying Factors Considerations used to convert Mineral Resources to Ore Reserves. These include, but are not restricted to, mining, processing, metallurgical, infrastructure, economic, marketing, legal, environmental, social and governmental factors.
MRE Mineral Resource Estimate
Mt Million tonnes
Ore The naturally occurring material from which a mineral or minerals of economic value can be extracted profitably or to satisfy social or political objectives. The term is generally but not always used to refer to metalliferous material, and is often modified by the names of the valuable constituent.
Ore Reserves Is the economically mineable part of a Measured and/or Indicated Mineral Resource. It includes diluting materials and allowances for losses, which may occur when the material is mined or extracted and is defined by studies at Pre-Feasibility or Feasibility level as appropriate that include application of Modifying Factors. Such studies demonstrate that, at the time of reporting, extraction could reasonably be justified.
PQ Diamond drilling bit and sample tube size resulting in 122.6mm diameter hole and 85mm diameter core.
PRP100 SGS sample preparation procedure where rocks are dried, crushed, pulverised and a 100g sub-sample produced for assay.
RC Reverse circulation
RCD Reverse circulation with diamond tail.
RCH Reverse circulation hydrology holes.
Riffle Splitter Manual sample splitting device to produce representative samples from larger sample (typically used with RC drill chip samples).
Strike The course or bearing of the outcrop of an inclined bed, vein, or fault plane on a level surface; the direction of a horizontal line perpendicular to the direction of the dip.
Whittle Optimisation The Four-X Whittle Optimisation process uses the Lerchs-Grossmann algorithm to determine the optimal shape for an open pit in three dimensions. Based on the economic input parameters selected it can define a pit outline that has the highest possible total value, subject to the required pit slopes.
Wireframe Three dimensional solids representing geological/mineralogical domains.
RNS may use your IP address to confirm compliance with the terms and conditions, to analyse how you engage with the information contained in this communication, and to share such analysis on an anonymised basis with others as part of our commercial services. For further information about how RNS and the London Stock Exchange use the personal data you provide us, please see our Privacy Policy.